原标题:电装的制造革新,目标为两个“减半”
丰田要推行全新的汽车开发方法“TNGA(丰田新全球架构)”。基于这一架构的汽车要到2015年之后才会登场。但在丰田集团各公司,部件通用化的具体效果已经显现出来。
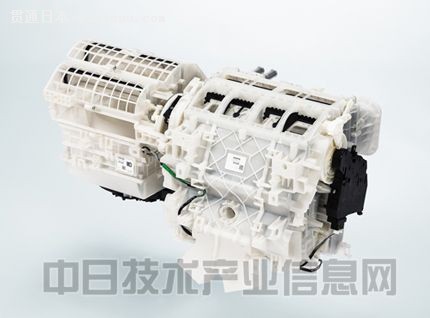
电装开发的新型汽车空调单元
丰田2013年11月推出SUV(多功能运动车)“猎犬”,2014年1月推出微型客车“NOAH/VOXY”。在这两款汽车上,丰田开展了前所未有的新尝试——共用空调单元。
负责空调单元的开发和制造的是掌握着全球3成汽车空调份额的电装。该公司2013年开发出了从“威姿”等级的小型车到高级轿车和SUV,大部分车型均可直接使用的全球第一款通用空调单元。今后还预定向丰田以外的其他汽车企业供货。
丰田已经开始推行名为“TNGA(丰田新全球架构)”的新车开发的新方法。虽然采用该架构的新车要到2015年以后才会问世,但在部件层面,这种方法的成效已开始显现。空调单元的通用化就是一个例子。
TNGA效应究竟是什么?这一点可以从电装瞄准的两个“减半”中找到答案。
第一个减半是指开发投入的人数和时间等资源减半。电装热设备开发1部开发2室主任栗山直久说:“因为开发时要设想到在今后推出的多款车型中配备,所以最初投入的资源会比较多,但随着配备车型的增加,效率会越来越高。我们希望最终能使开发效率提高1倍。”
使汽车必不可少的组成部分、存在已有数十年之久的空调的开发效率一下子提高1倍。这也可以看出此前的开发效率之低。
空调单元嵌在驾驶席的内饰部件——仪表板的内部。不同车型的仪表板内部的结构不同,必须根据具体的结构开发空调单元。而且在最近,车载导航仪类等信息设备也在仪表板内“称霸一方”,留给空调的空间就更小了。
而另一方面,要想提高汽车的燃效,必须设法节约电力,为了满足中途发动机会停止的HV(混合动力车)等的需求,静音化也必不可少。对于生产车载空调的企业来说,为了确保微薄的利润,就必须耗费大量的劳力。
“解放”备受虐待的空调
开发任何车型皆可配备的空调单元意味着“解放”备受虐待的空调。
此前,丰田使用相同底盘的车型已经实现了空调单元的通用化。但丰田的底盘种类繁多,派生款式也为数众多,这就需要开发并生产很多“特别规格单元”。
这些单元怎样才能实现通用化?电装从2009年前后开始就一直在探讨。在这一过程中,丰田提出TNGA方针,一举加快了通用化步伐。
通用化是经过丰田与电装的不断争论而实现的。电装要凝聚了自身拥有的技术经验,最大限度推进小型轻量化和高性能化。丰田则要维持基本设计,使不同的车型能够配备相同的空调单元。满足这两点,就能实现通用化。
为了更加深入地了解丰田对空调的要求,电装把过去曾负责丰田业务的技术部的工程师调到了空调开发组。相反,精通空调技术的工程师则被调到了负责丰田业务的技术部。进行了史无前例的人事交换。
电装发挥自身和集团公司大部分核心部件均为自行生产的优势,从部件层面重新调整设计,使体积比原有产品缩小了20%。这很大程度上是因为通用化带来了部件层面的量产效果,使新的开发和生产投资成为了可能。栗山主任说:“如果没有TNGA不破坏通用化所需设计这个前提,这一点恐怕很难实现。”
重新编织解开的线团
另一个减半发生在工厂,即电装在日本的空调主力工厂西尾制作所。电装提出了把新型空调单元的生产线面积缩小一半的目标。
电装之所以在TNGA浮出水面之前,就开始实施通用化,也是为了解决生产成本方面的课题。虽然丰田的汽车通过采用相同的底盘,推行了空调通用化,但其他企业的空调还是因车型而异,必须分别生产。
为丰田制造部件的“丰田生产线”通过采用机器人,自动化已经达到了一定水平。但是,由于向其他企业供货的数量少,“其他生产线”上的多个款式只能依靠手工作业来组装。要想继续在人工费高昂的日本生产,就必须改变这些效率低的部分。
新型空调单元以丰田的汽车为中心,能够配备的车辆将一举扩大。因此产量也达到了过去的几倍,容易推进伴随大规模投资的机器人自动化。今后,自动化率将从现在的70%左右增加到100%。
机器人难以完成的线束安装虽然还要依靠手工作业,但今后,这些工序也将实现自动化。电装将把这种集合了最先进生产技术的生产线打造成“全球标准生产线”,逐步推广到海外工厂。
另外,在生产方面,丰田的整车工厂也能从中受益。随着空调单元通用化程度的提高,即使生产线上的车型改变,也可以安装相同的空调单元,可减少库存量和库存空间。
TNGA的真正价值是在供应链上引发的这些连锁反应。随着空调通用化的推进,电装的下游分包制造商也能够提高开发和生产效率。倘若进展顺利,分包制造商制造的部件还可以销售给其他的空调企业。
TNGA看上去就像是在解开过去通过工作纠缠在一起的巨大线团。的确,最初的作业伴随着困难和沉重的负担。但是,如果顺利解开线团,重新编织成最佳的图案,或许将会为整个丰田集团创造出巨大的利益。(作者:熊野 信一郎,日经技术在线!供稿)